Craft Beer: The Challenge of Sustainability
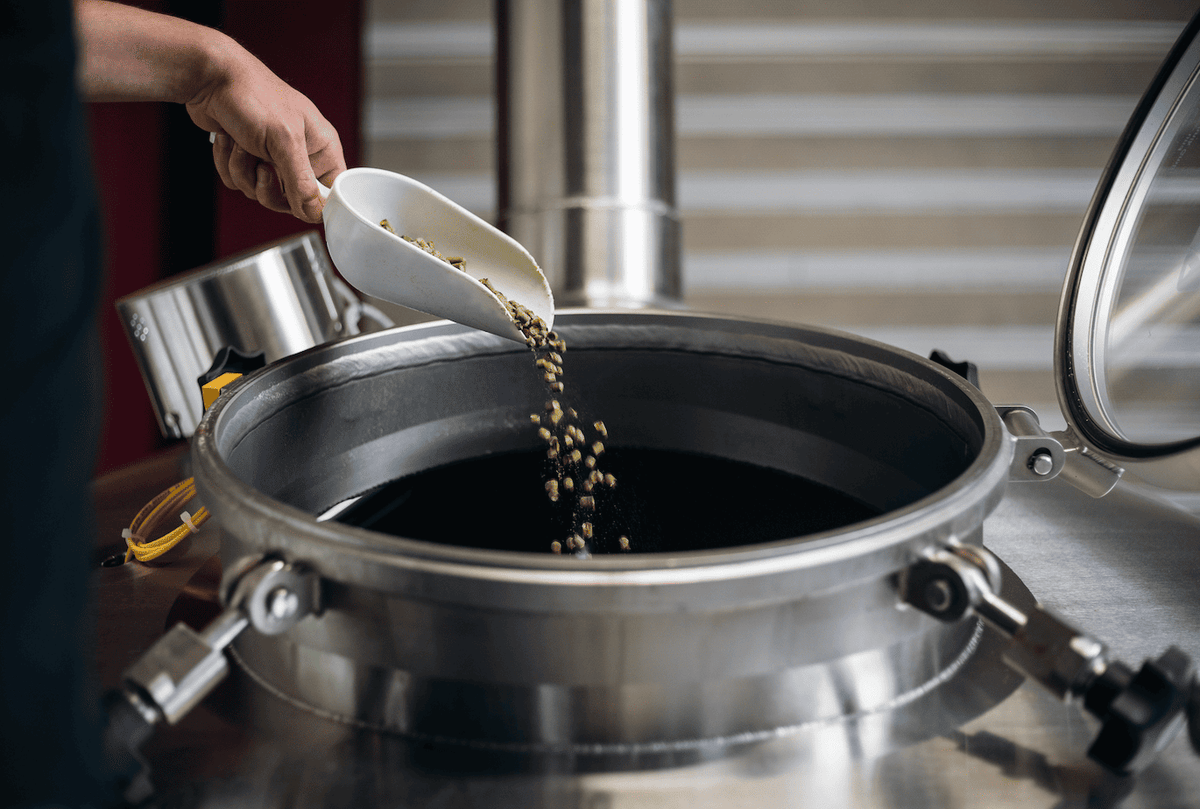
Craft beer production isn't just a matter of recipes and traditional know-how. Today, it's a real technical and environmental challenge that's forcing brewers to completely rethink their production methods. The challenges are numerous: water consumption, energy costs, waste management, raw material transportation, and more.
Faced with these challenges, the craft brewing sector is innovating and reinventing itself, proving that it is possible to produce exceptional beers while respecting the environment.
Responsible management of natural resources
Water, an essential component to preserve
Water makes up over 90% of beer, making it naturally the brewer's most valuable ingredient. To produce one liter of beer, traditional breweries use an average of 5 to 7 liters of water. Modern craft breweries have significantly reduced this consumption thanks to significant technical innovations.
Water recycling and reuse systems have been improved: closed-loop cooling circuits that allow cooling water to be reused, optimized cleaning systems that reduce consumption during washing phases, recovery of process water that can be reused for certain ancillary operations. These innovations now allow the most efficient breweries to go below the 4 liters of water per liter of beer produced mark .
Zepp , a craft lager with delicate floral notes , perfectly illustrates this economical approach. Its production uses particularly water-efficient brewing processes, notably thanks to a system for recovering the rinsing water from the spent grains, which is then reused for cleaning the equipment.
Intelligent recovery of co-products
Spent grains, the malt residue left over from brewing, represent a considerable volume: for every 100 liters of beer produced, approximately 20 kg of wet spent grains are obtained. Rich in protein (up to 25%) and fiber, they are an excellent feed supplement for livestock. Their use as animal feed creates a true symbiosis with the local agricultural land.
But the possibilities don't stop there. New avenues for recovery are emerging: composting, biogas production, incorporation into human food in the form of flour... Craft breweries are exploring these alternatives to optimize the use of their co-products.
Energy optimization: from theory to practice
Equipment redesigned for greater efficiency
Energy consumption represents a major cost in beer production. Brewing requires heating and cooling large volumes of liquid to precise temperatures. Next-generation equipment incorporates innovative solutions to reduce this consumption:
- Reinforced thermal insulation of brewing tanks which limits heat loss
- High-performance heat exchangers that recover heat from boiling wort to preheat the water for the next brew
- Digitalized control systems that optimize heating times and temperatures
- Variable speed refrigeration compressors that adapt their consumption to actual needs
These innovations can reduce the total energy consumption of a modern brewery by up to 30%. Investing in this equipment represents a significant initial cost, but its efficiency allows for a rapid return on investment, typically between 2 and 4 years depending on production volumes.
Double Oat , our double IPA with exotic mango notes , benefits directly from these innovations. Its production, which requires precise temperatures to preserve its complex aromas, relies on this latest-generation equipment.
Architecture designed for sustainability
Energy efficiency begins with the very design of brewery buildings. The principles of bioclimatic architecture are now integrated from the design phase. The goal is to create a production environment that naturally minimizes energy requirements while optimizing working conditions:
- Optimal orientation of buildings to take advantage of natural light and reduce lighting requirements
- Reinforced insulation of walls and roofs which limits heat loss
- Rainwater harvesting systems that reduce drinking water consumption
- Natural ventilation that improves thermal comfort while reducing air conditioning needs
These architectural choices, combined with high-performance equipment, create an optimal production environment where every resource is used wisely. A well-designed modern brewery can thus reduce its environmental footprint by 40% compared to a traditional facility.
Local commitment: the pillar of responsible production
Short circuits, an economic and ecological obviousness
Choosing short supply chains goes far beyond a simple marketing argument. It offers concrete and measurable advantages:
- Significant reduction in emissions from the transport of raw materials
- Better traceability of ingredients
- Ability to respond quickly to quality variations or supply issues
- Support for the local economy and maintenance of traditional know-how
Close collaboration with local producers also fosters innovation . Stirling , our gluten-free pale ale , is a perfect example. Its development required extensive work with our suppliers to select and adapt raw materials while ensuring a total absence of gluten.
Partnerships that build the future
Establishing lasting partnerships with local stakeholders—farmers, maltsters, and distributors—helps optimize the entire production chain. These collaborations extend far beyond the commercial sphere to create a truly virtuous ecosystem:
- Joint crop planning that guarantees the supply of quality raw materials
- Sharing knowledge and best practices that benefits the entire sector
- Pooling of resources that allows economies of scale
- Development of innovative projects that advance the entire sector
Towards ever more responsible production
Environmental commitment in craft beer production is no longer an option but an imperative. Microbreweries, thanks to their human scale and flexibility, play a key role in innovation within the sector. Every technical improvement, every new solution implemented brings the brewing industry closer to a more sustainable model.
This transformation requires significant investment and a long-term vision. High-performance equipment, recycling systems, and optimized infrastructure represent significant costs. But this commitment is essential: producing exceptional beers can no longer be conceived without careful consideration of their environmental impact.
The future belongs to breweries that can combine taste excellence with environmental responsibility. This evolution is not a barrier to creativity - on the contrary , it encourages innovation, rethinking processes, and imagining new solutions. Sustainability thus becomes a driver of innovation that benefits the very quality of the beers produced.